It’s easy to move on from oxy/acetylene welding in the shed to oxy/LPG
By Greg Holster
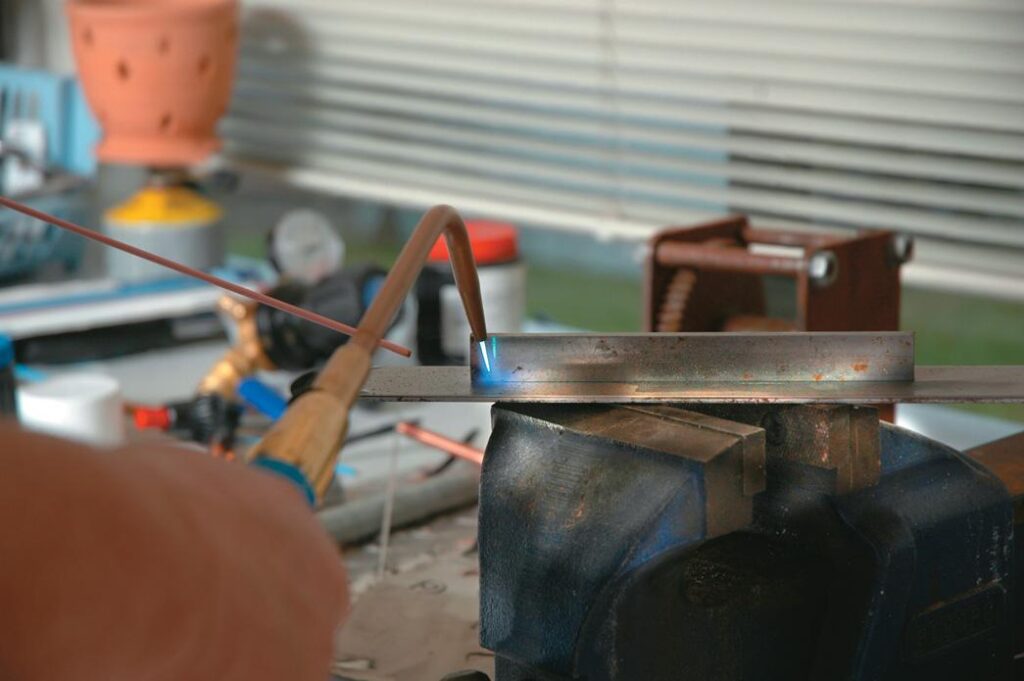
Many sheddies weld and cut with the oxy/acetylene, a gas combination that has been widely used in home workshops.
Long before MIG welders or fancy plasmas came onto the scene, the art of welding, cutting, and brazing was to work with gas. The hire or exchange cylinders used by sheddies invariably were oxy/acetylene as this was one of the most common processes for welding, cutting, or brazing.
But there is an alternative–liquefied petroleum gas (LPG) and oxygen. This combination can be used for heating, bending, brazing, soldering, silver soldering, and flame gouging to name just a few applications.
There is a certain amount of conjecture out there when it comes to the advantages and disadvantages, costs, heat, speed, and equipment when using oxy/LPG at home or in the shed. Hopefully, this article will help clear up some myths around what can and can’t be done, the basics behind the process, getting set up, and some of the basic differences.
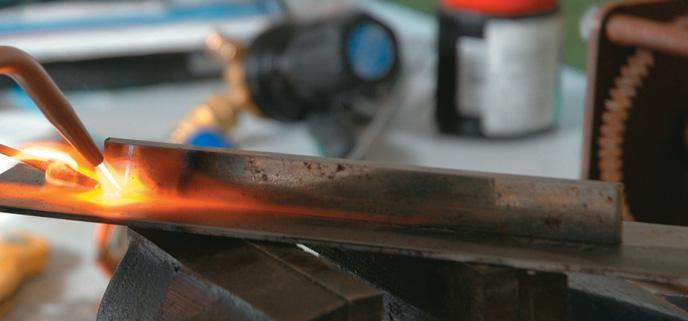
LPG
In New Zealand, LPG is often referred to in engineering circles as propane because New Zealand
LPG is made up of a mixture of mostly propane and butane. The butane ranges from around 40 percent down to around 10 percent, the usual proportion. A pungent-smelling organic compound called ethanethiol (CH3CH2SH) is added to LPG so that leaks can be detected. Without this additive, it would be almost odorless.
LPG is usually derived from fossil fuels, usually by refining crude oil or by being extracted from oil or natural gases as they come from the ground. At atmospheric temperatures and pressures, LPG will evaporate; that’s why it’s stored as a liquid to be transported in steel cylinders, the most common being our domestic 9 kg cylinders. The cylinders can be stainless steel (or aluminium if you have the money to spend on an expensive gas tank).
Pressure
A certain amount of gas vaporizes inside the cylinder but the pressure it creates in the top part of
the cylinder is enough to keep the balance in a liquid state. These cylinders are filled only to between 80-85 percent of their capacity to allow for expansion when the temperature rises.
Vapour pressure is the pressure at which LPG becomes a liquid. This may vary depending
on the butane content and temperature. The standard pressure in the cylinder is 700 kPa (100 psi) @ 15 ºC.
LPG is also heavier than air and will flow into low-lying areas such as drains, basements, or garages. Apart from the obvious danger of ignition or fire, suffocation is also a hazard that is often forgotten And for you tree-hugging sheddies, LPG has the least carbon-emitting hydrocarbon fuel percentage, approximately 20 percent less CO2 per kWh than oil, approximately 30 percent less than coal and more than 50 percent less than coal-generated electricity.
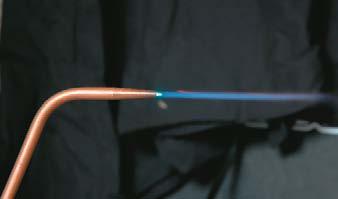

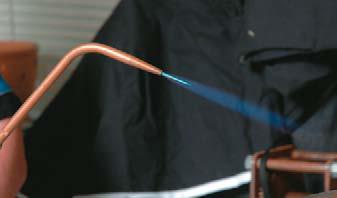
“So the old “she’ll be right” might kill you. Beware.”
“Many people changing their gas welding don’t change over to an LPG hose until the acetylene hose has to be replaced. If you do this, examine your hoses often—you won’t want to end up as a human BBQ.”
“For cutting, though, the tip must be changed. Using the wrong cutting tip with the wrong fuel gas could, and probably will, spell trouble.”
Flame heat
The advantage of the oxy/acetylene mix is that acetylene produces the highest flame temperature of all the fuel gases. When combined with oxygen at the welding tip, the maximum temperature is approximately 3160 °C. LPG when combined with oxygen produces a slightly lower flame temperature than acetylene, up to a maximum of 2810 ºC.
Propane has a greater stoichiometric requirement (the quantitative relationship between reactants) for oxygen than acetylene does. For the maximum flame temperature in oxygen, the ratio of the volume of oxygen to fuel gas is 1.2:1 for acetylene and 4.3:1 for propane.
Regulators
Unlike an acetylene regulator, LPG regulators have only a delivery pressure gauge. The reason is that LPG is a liquid in the cylinder so is at constant pressure until the cylinder is empty. Neither the acetylene nor the LPG regulators should be modified to attach to the opposite gas, especially hooking up an LPG regulator to acetylene.
Acetylene is never used above 100 kPa (15 psi) while LPG regulators can be adjusted way beyond acetylene’s safety threshold. So the old “she’ll be right” might kill you. Beware.
Acetylene has a left-hand 5/8 inch BSPLH (Type 20) regulator while LPG / propane has a 0.88 inch 14 NGO left-hand regulator. Up until about 20 years ago, the threads were the same but for obvious safety reasons, this was changed.
Hoses
Acetylene hoses are usually red or maroon and LPG hoses are orange, to distinguish them. The difference is in the inner tube. The acetylene hose is usually black styrene/butane rubber, and the propane hose black nitrile/butadiene rubber. Hoses have a limited life. If by chance the wrong gas is used, these hoses will perish and rupture prematurely.
Many people changing their gas welding don’t change over to an LPG hose until the acetylene hose has to be replaced. If you do this, examine your hoses often—you won’t want to end up as a human BBQ.
How much?
A question I get asked a lot is how much brazing, heating, or cutting can be done with a small oxygen cylinder and a full 9 kg BBQ cylinder?
Remember, LPG uses a higher oxygen ratio than that of an oxygen/acetylene mixture. For this
process, we are using a Number 15 LPG tip. Let’s assume we have a full 9 kg LPG / propane BBQ cylinder. There is a 9 kg weight of liquid gas which equates to 17.6 litres by volume of liquid LPG (liquefied petroleum gas). If we convert that to gaseous LPG we get 4.7 cubic metres or
4700 gaseous litres of LPG.
Our Number 15 tip uses 6.5 litres per minute of each of LPG and oxygen. If we set our gas pressures at 50 kPa each for LPG and for oxygen, our 9 kg cylinder should last for 723 minutes of actual gas, a tick over 12 hours. I’d be happy with 700 minutes.
A “D” size (small) oxygen cylinder contains 1.5 cubic metres of compressed oxygen which equates to 1500 litres of gas. So at 6.5 litres per minute flowing through our Number 15 tip, we have approx 230 minutes of welding/brazing time. Call it 220 mins (3 hours 40 mins) with a pressure drop at the end. That’s plenty of time to learn to master this process.
Fusion welding
Fusion welding with oxy/LPG is considered impossible but this is not quite true. It can be done, but the end product is basically a heavily carburised piece of steel. This comes from the fact that the oxy/LPG flame, apart from being lower in temperature, is also less focused. Oxy/acetylene during combustion creates a CO2 shield which reduces the oxidization effect. This shield is absent from oxy/LPG.
Converting from acetylene
Let’s assume you have an oxy/acetylene gas set. How do we convert this without spending a zillion dollars?
Firstly, assuming your handpiece is in good condition, you will need to establish if it is compatible
with an oxy/LPG setup. Most sets are. The Cigweld Comet 3 and the majority of copies made to imitate it should be OK to use. If you are not sure, ask your local industrial gas company or welding outlet.
The things that need changing if you are already set up for acetylene are the regulator, the gas hose, and the tip. But try welding tips first— you may be happy with the way they perform. A standard Number 12 tip was used for the copper tube illustrated here and worked fine. They don’t like wind though. Acetylene tips can blow out easily.
For cutting, though, the tip must be changed. Using the wrong cutting tip with the wrong fuel gas could, and probably will, spell trouble.
Lighting up
LPG has almost half the flame velocity in oxygen that acetylene does, so this means it burns more
slowly as it leaves the tip. For this reason, LPG brazing tips are notched back, as illustrated. This
allows for a much more stable and secure flame.
Proper LPG tips are easier to set and much easier to light. Standard tips can be used but the lighting and setting procedure can be tricky. It shouldn’t be dangerous, but if you have flashback arrestors all the better. These are a great “seatbelt” against both little and big accidents.
Lighting up is the first big difference you will notice. Because LPG is heavier than air, the tip should be pointed downwards. Make sure after setting your pressures that you open the valves and purge each line. We don’t want any mixed gases in our hoses.
We will be using 50 kPa (7 psi) each with our Number 15 tip. Open the torch valve slightly and
light using a flint lighter, not a cigarette lighter. Hold it approximately 50 mm from the tip but
inside the stream. Once the torch is lit, increase the flow until the flame is burning approx 15-20 mm away from the tip.
Now hold the tip against the workpiece or piece of plate. This will keep the flame stable while coming back onto itself. Then open the oxygen valve until the desired adjustment is obtained.
Acetylene flame is orange and has a straight trajectory. The LPG flame is more transparent and seems to swirl slightly. If you allow too large a flame before adding the oxygen you may snuff the flame out, hence the 15-20 mm gap once it is lit.
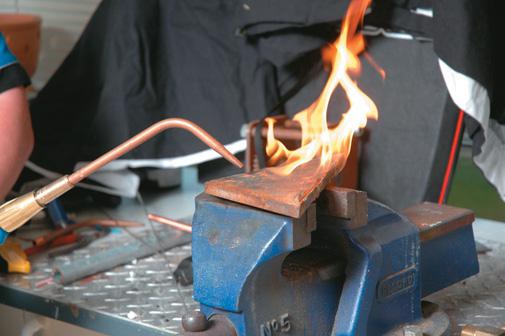
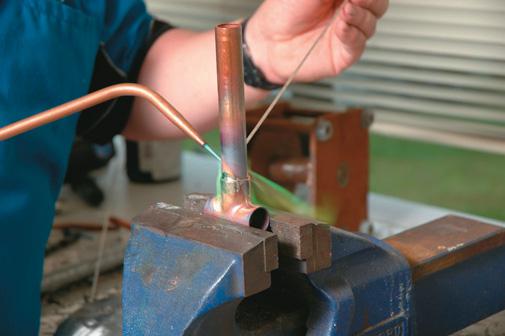
Flame adjustment
Accurate flame adjustment and settings are the most important factors in making any welding or
brazing successful. Because the oxy / LPG mixture uses more oxygen in its ratio (4.3:1) the flame will have a bluish highly oxidizing appearance. But it is not as oxidizing as it may appear when compared with an acetylene flame.
So we have our torch alight with hopefully no singed hairs—yes we’ve all done it. Now the more oxygen you add, the shorter the cone will get. Add or reduce oxy until the inner cone is pointed and bluish in colour. The cone should have a clean defined edge but will be a lot longer than the acetylene, say 25-30 mm long. The flame will also have a nice roaring sound. Don’t let this sound fool you. The roar makes the flame sound hotter than it is.
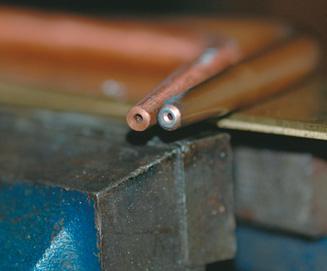
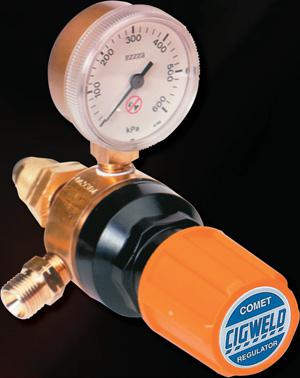
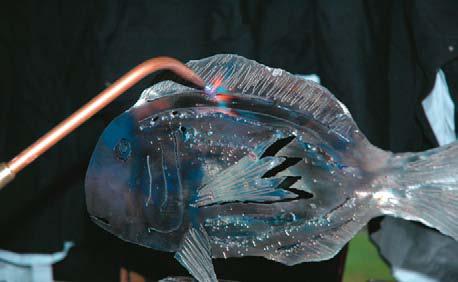
Brazing
Brazing is where I think that oxy / LPG comes into its own, especially, if you aren’t an expert at it. The filler rod doesn’t require a molten pool, just a heated surface at 900 ºC for bronze and around 600 ºC for our silver brazing alloys. This can make brazing far easier to grasp and control.
Often when you are using oxy/acetylene it can be very easy to use too much heat or have the heat get away from you. The end result can be burning the weld, burning the flux, using too much filler rod, or all three at once, usually resulting in a large bronze lump or hole. Been there, done that. Flux-coated rods can help you avoid this, by the way.
Brazing with oxy / LPG means you will have more time to see the temperature come up. This is signaled when any flux you are using goes clear. Dip the bronze or low-temperature alloy onto the material and the flame and filler will do their own thing.
You will find that you need to move at about the same speed as for oxy/acetylene, possibly slightly
slower. The pre-heat may take a little longer, but on thin material or small jobs, you will never notice the difference. If you normally use a Number 12 tip, go up a size to Number 15.
The proof is in giving it a go. I have used oxy / LPG in my shed for more than 20 years so I am biased anyway. It has done almost everything I have ever needed to do with a gas set.
If I ever weld with oxy/acetylene these days, it’s for training or an article for The Shed mag. But there is something to be said for the speed and heat of acetylene.
Yes, you will still have to rent or own an oxygen cylinder but you can always find your fuel gas under the barbie.
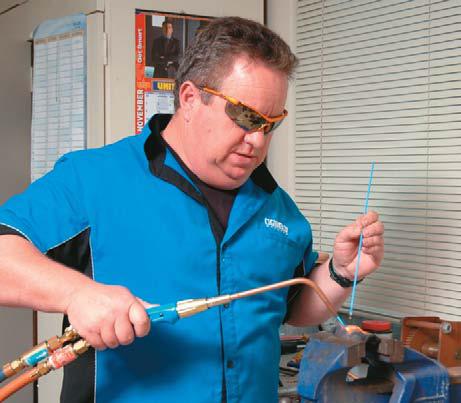