Size isn’t everything
A Jack of all trades with the heart of an Italian
This February/March 2024 issue 113, we visit a whole bunch of sheds around NZ and in fact all around the world. We start with a profile of the talented Auckland sheddie Chris Elliot.
Chris has a small shed in Central Auckland from where he restores Italian scooters and cars, well, cars that don’t take up a lot of space such as Fiat Bambinas. With a background in movies and TV set design, Chris is never idle and not only restores all the Italian autos he can but gets his creative side going with household artefacts as well. One talented sheddie.
Jason Burgess writes “A cinematic late-afternoon light pours through the corner window of Chris Elliott’s vest-pocket shed. The miscellany of collected artefacts, fabric, and vehicular memorabilia conjures up a neat yet cluttered bazaar in some exotic foreign land rather than an active workshop on the fringe of Auckland City. This concrete single garage is a celebration of creativity and productivity. Swinging a cat – or, for that matter, a hammer – might seem problematic in such confines but, when it comes to fulfilling a wide array of job briefs and cross-disciplinary commissions, Chris somehow makes things come together.”
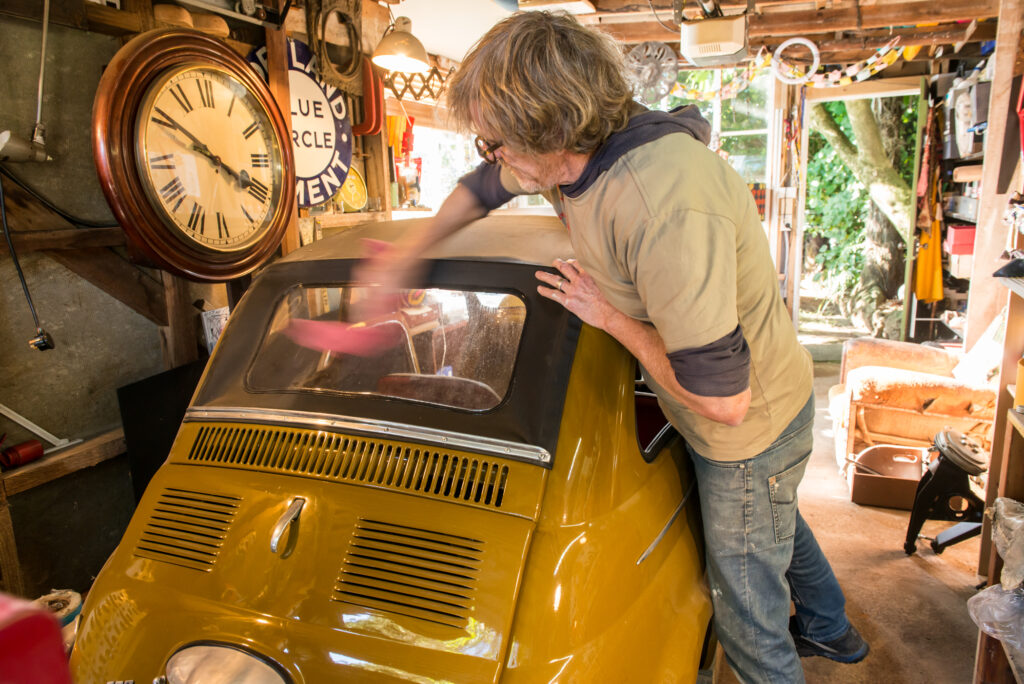
Behind the shed door
Self-drive shed tours – along the lines of the popular garden tours – may well become a regular pastime
What could be better for inquisitive sheddies than a shed tour of workshops in your town. Well, the first one of these types of tours has just taken place in Christchurch and The Shed went along for a nosey.
“We then travelled north of Christchurch to visit the shed of engineer Graeme Topp. Until a few months ago, this was the premises of Graeme’s business, which worked on the machinery of commercial bakeries. Another business, which he has retained, makes parts, such as bars and exhausts, for Triumph motorcycles, using a robust tube-bender and an Australian Nuttall lathe.
The shed is now the home of several vehicles, mainly Austins, which Graeme is starting to restore. Dominating the space is a 1920s Graham-Paige, which is associated with a quite bizarre story.”
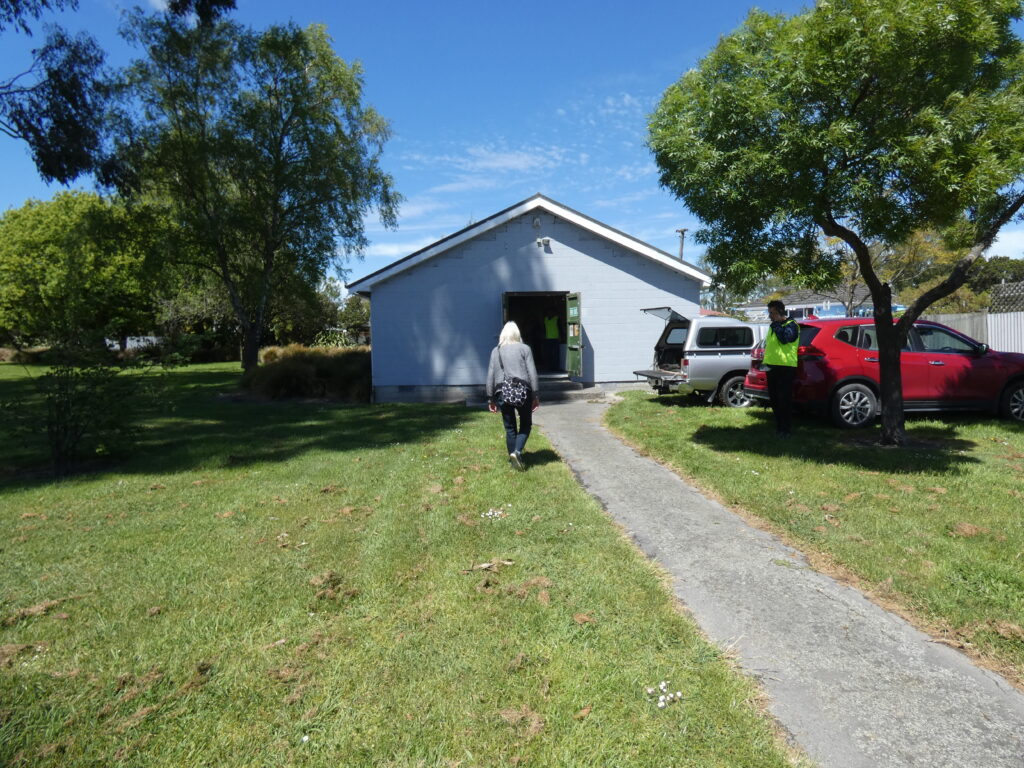
From the archives – Making a linisher
Constructing the “most used tool in the shed”
Leif Haseltine is a very busy guy in his workshop from where he runs a very successful knife making business, Haseltine Knives – [email protected]
Leif often finds that he can’t always find the correct tool to do some of the various tasks involved in creating the ultimate product. What to do? Make your own tools and adapt it so it does all those little tasks just so. Here he creates his own Linisher and shows us how he goes about making it just right for the job.
“I needed a belt grinder/ linisher for knife-making. A large range of tasks is involved in knife-making, and most of the affordable, commercially made machines are unsuitable. They would be good for only one task; if I were to buy, I would probably have to buy two or three of them.
I decided I would make my own, with changeable tooling heads; that would allow me to make additional heads to fit it later.
I wanted to use different-sized belts on it, one being 50x2745mm. This is easy to get and has a good range of grits available. It is a long belt, so it is cooler when it grinds and I get more knives per belt.”
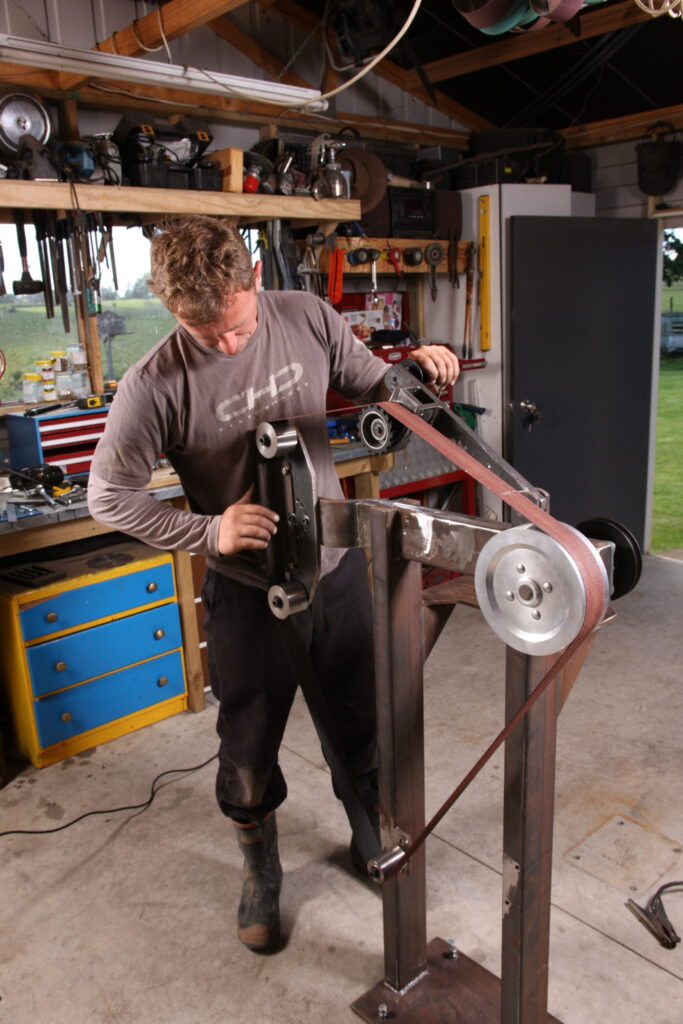
Electronics: Introduction to Arduino UNO R4 (Playing chess) – part 1
Arduino has produced an update to its popular UNO R3 board; in this series Enrico Miglino and Luis Garcia show how UNO R4 can be used to run a chess engine.
“For Arduino, 2023 was a very notable year.
After several agreements and partnerships with industrial brands such as Bosch for the Arduino Nicla, the Arduino platforms are expanding, moving from being a popular board for hobbyists and makers to entering the world of industrial applications based on embedded devices.
The ‘classic’ version of Arduino UNO R3, based on the AVR 328p, survives, and probably will for many years. However, the most recent Arduino boards implement powerful Arm-based microcontrollers oriented to IoT and embedded machine learning (ML) applications.”
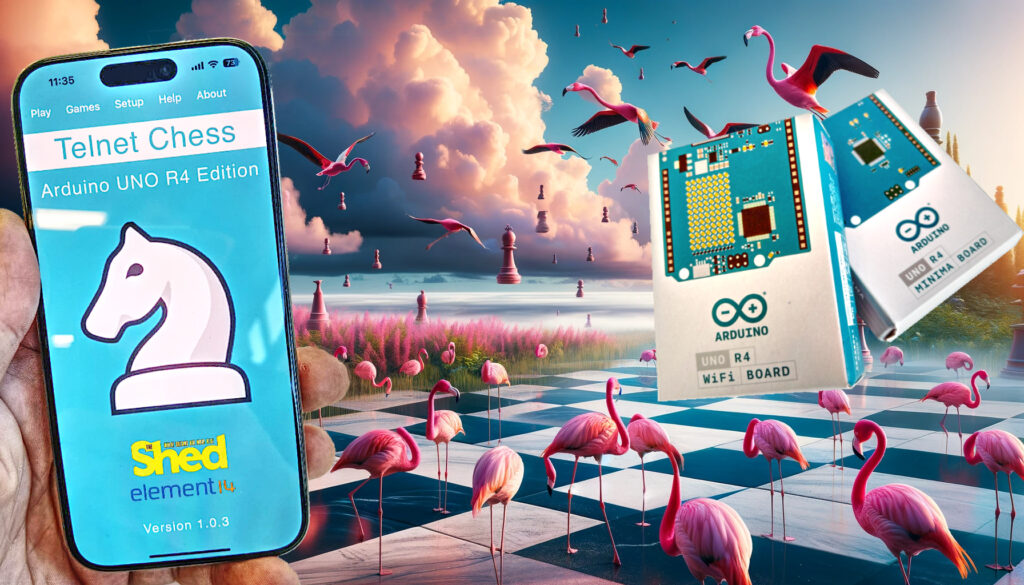
House relocation
Eleanor’s journey – the great relocation (part 1)
We’ve all seen the ads “House for relocation – for not for very many dollars”.
A cheap house by the sound of it. Well one of our Shed team, Andrew Broxholme, took up just one of these opportunities and shares the highs and lows of relocating a hundred year old bungalow near Whakatane onto his back section at home. How hard could it be, right?
“So, you are thinking of relocating a house to your property; or, you want to build but, having seen those house-relocation shows, you’re thinking it might be a good idea just to move an existing house – perhaps to get a house for less, or because it might be quicker than building from scratch? Well, keep reading.
My wife and I moved the lovely old house you see pictured here to our land last year, but it turned out to be way more stressful and much more expensive than expected; it also dragged on for more than nine months. After the relocation, we talked to others who had done the same. Pretty much everyone said they would never do it again. Would we? Well, that depends – if you keep reading, you’ll find out why.”
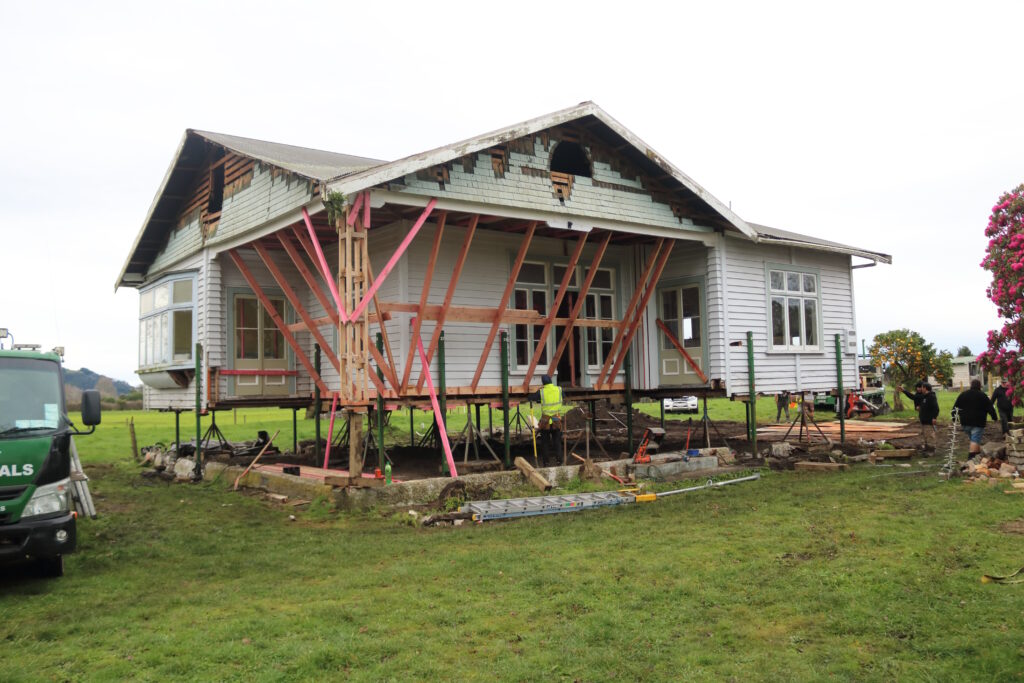
Project – a musical workstation
A weighty project brings its own challenges, but the result gratifies both creator and client
Regular Shed contributor Nigel Young took on a weighty commission for a local client, building a sound desk – a synthesiser and piano keyboard workstation. There was a lot to consider and the client needed it to suit all his creative needs so Nigel got stuck into what was quite a time consuming and tricky build of a sturdy working desk.
“An opportunity to build a bespoke sound desk came my way recently – one that on the one hand was relatively simple, while on the other hand was very specific in its design, demanding a very high quality of finish.
It started with some sketches, a walk through a local hardware store to determine the materials required, a ride on my Kawasaki W650 to see the equipment that had to be accommodated, 3D drawings in SketchUp to see how it would all come together, and a lot of emails just checking and refining the details.
This would be a project about logistics, priorities, and process – with a few surprises on the way past.”
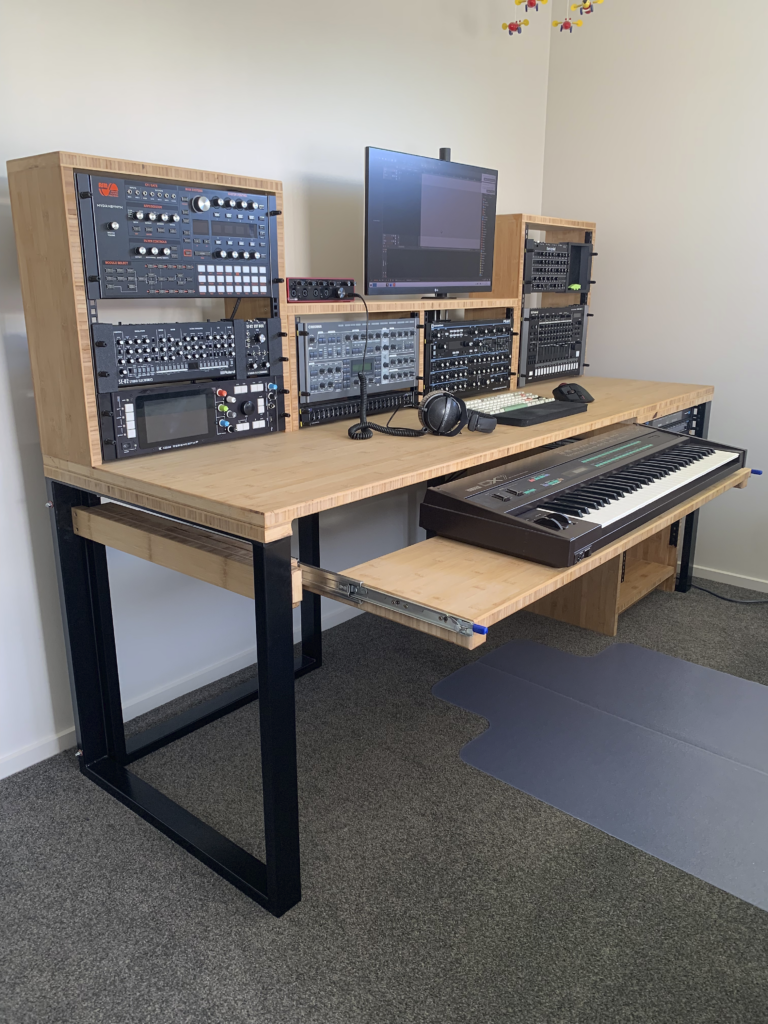
Another shed!
Letting the imagination run wild led to an innovative solution to a challenge – and resulted in a magical space
You know how it goes, you build yourself a shed to do all your clever stuff in and have a space for oneself. Then your better half goes, “That looks awesome, can you add on a space for me please?” Then as the children grow and their creative juices start flowing they ask for a space as well. So how about the whole family gets stuck in and gives a hand? Well for Scott Gavin, this is exactly what happened. He now has a large shed for all the family with private zones and built by his now family of sheddies. Nice.
“Why build yet another shed? Was I bored? Do I have copious amounts of spare time? To spend lots of money?
The respective answers are: No; NO!; and Absolutely not!
So why?
Well, my wonderful wife has spent many years perfecting her skills as a potter, and later a jeweller. Our house is full of colourful pottery pieces and stunning silver creations. However, my garage was also filling up with pottery tools, bags of clay, buckets of glaze, and even a very large kiln. The decision was made to build my wife a pottery shed.
This was a significant project, but it turned out to be the most wonderful creative space, and a great place for her to hide from me and the kids.“
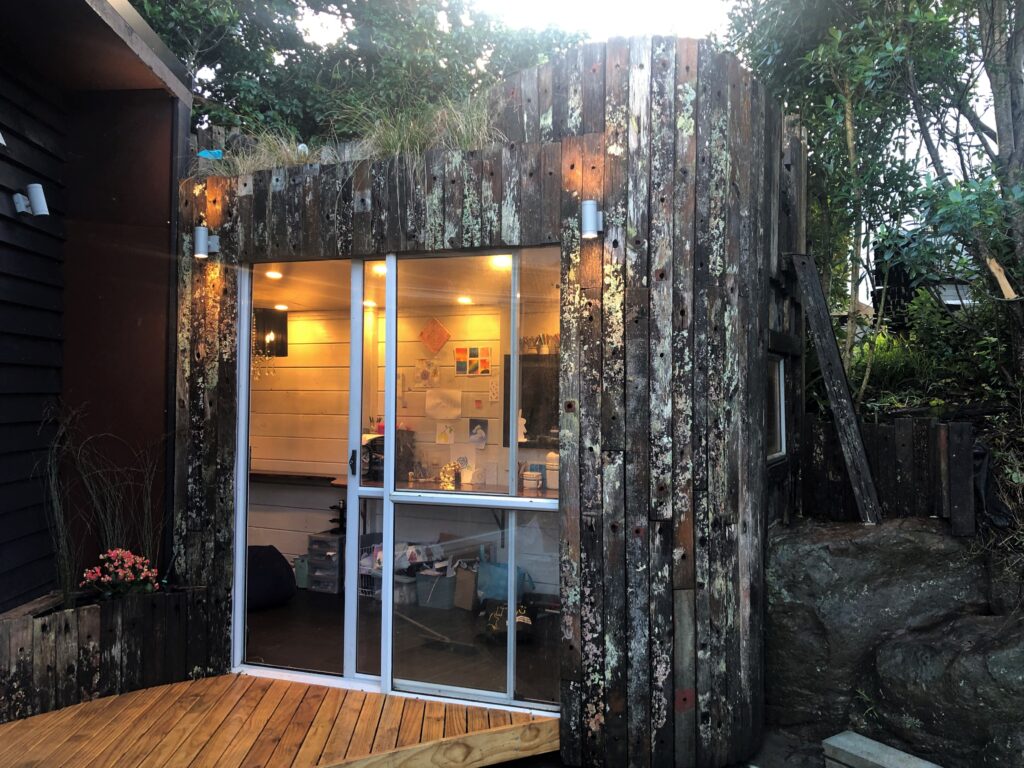
Off the grid – The right to repair
Repairability, reliability, and the push for a circular economy
When you live off the grid as Murray Grimwood does, it’s a case of repair rather than replace where you can. Murray is a huge advocate for this approach and so it seems so are millions more around the world attending Repair Cafes. There are now 50 of these cafes in NZ and in this issue we look at the huge success that Repair Cafes have become.
“The first Repair Café in New Zealand was run by the Lyttelton Harbour Timebank at Diamond Harbour School in 2013. There are now more than 50 in this country, and Repair Café NZ claims that 451 volunteers have spent 12,125 hours at 233 events; no minor effort. Bikes are the most common item repaired. Being involved would be a natural fit for many sheddies, and I would have thought there was a compatibility with Menzsheds, too.”
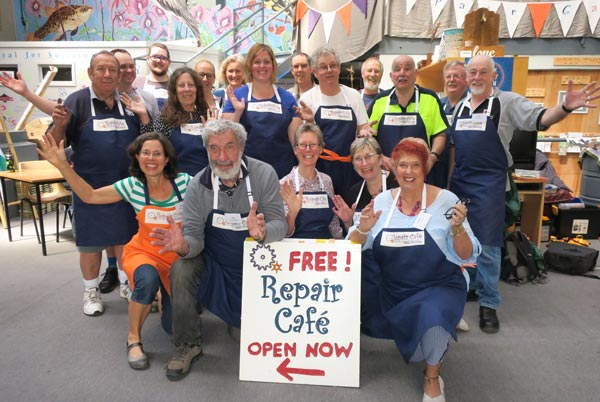
Make a catapult
Will the children of today ever enjoy the satisfaction of making something themselves?
Back in the day it was just as much fun to make your own toys as buying them. And, often, there was no choice – make your own toys or have none! Coen Smit makes a catapult like the one he made when a youngster, just for fun.
“The parts required for the old-fashioned catapult were simple: a stout forked tree branch, some rubber, twine, and a patch of leather. The rubber often came from a discarded inner tube (preferably from a car, as the rubber had better elasticity than a push-bike tube) and the leather patch from an old belt, shoe, or whatever came to hand.
To do this little adventure the justice it deserved, I used only the tools I had available as a child: a saw, a knife, scissors, a fretsaw, and sandpaper.”
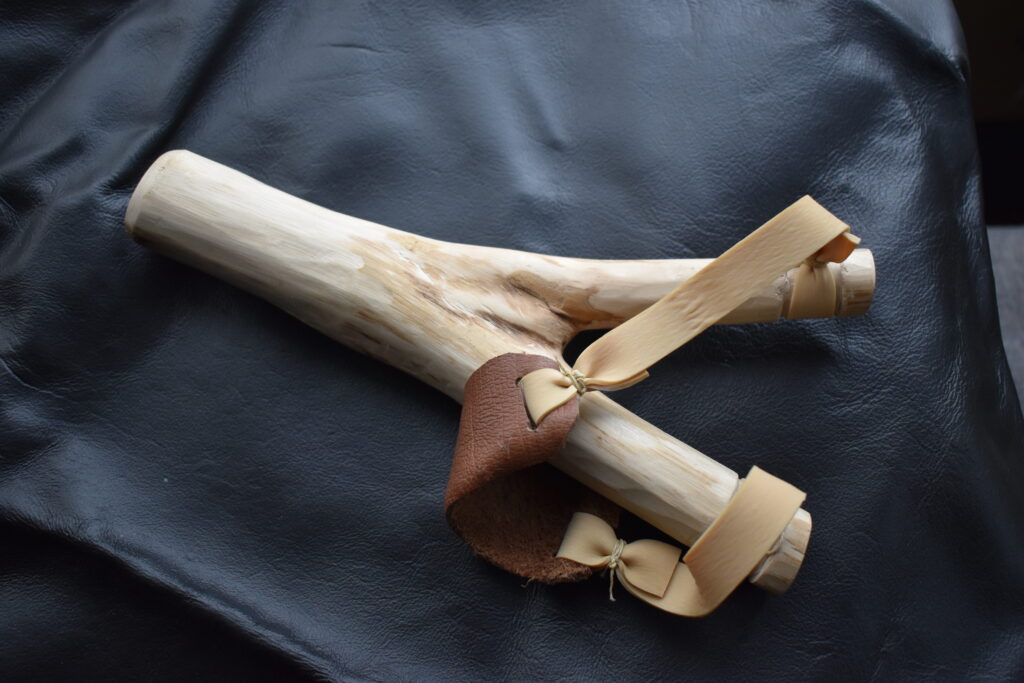
Power-tool racing
Diverse projects, created with the help of the circular economy
Back in The Shed issue 109, our electronics guru, Enrico Miglino, visited a Makers Fair in Belgium and was impressed by the power tool racing on show. Christchurch sheddie Chris Gordon saw that article and thought “I could do that”. So he did and on show here are the tasty power tool racers made in his shed and more. He’s one busy sheddie is Chris.
“Chris originally intended to use angle grinders, as most of the racers in Enrico’s photos did, but it turns out that angle grinders are popular items at the EcoShop – there were none for sale. What they did have was 14 chorded skill saws, so he bought two identical Black and Decker saws for, he thinks, $20. He also purchased a number of 7-inch circular-saw blades and a couple of pairs of inline roller skates, which provided the front wheels of the racers. The rest of the materials came from his own workshop. It turned out that everything that was needed was on hand.”
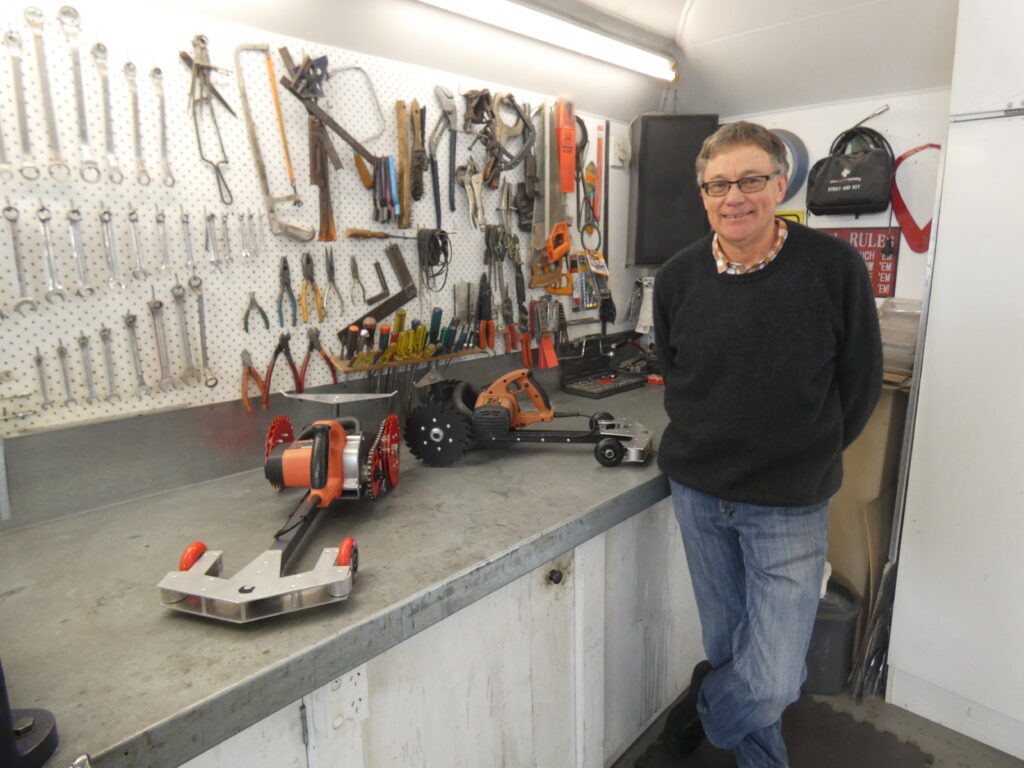
Building a cement shed
Fun with ferro-cement
Our favourite USA-based sheddie, Bob Van Putten, lives off the grid and enjoys having a crack at projects that he knows very little about so he can grow his skill base and learn along the way. This building of a ferro cement shed is just that and he enlists the whole family to help him out and so they can learn and enjoy this project as well. The family that builds together…
“I thought the structure would benefit from having the first coat applied all in one day, to avoid cold joints between batches of cement, so I rounded up some help. I had three adults and two kids plastering while I shovelled and mixed cement.
The adults on the crew complained: too dry a mix, too wet a mix, it isn’t sticking so I’m dropping more on the ground than getting on the walls, and ‘Why can’t you build normal stuff like everyone else’? In other words, all the usual adult hangups.
The kids had no trouble and dived right in. Being kids, they still knew how to play with mud and have fun.”
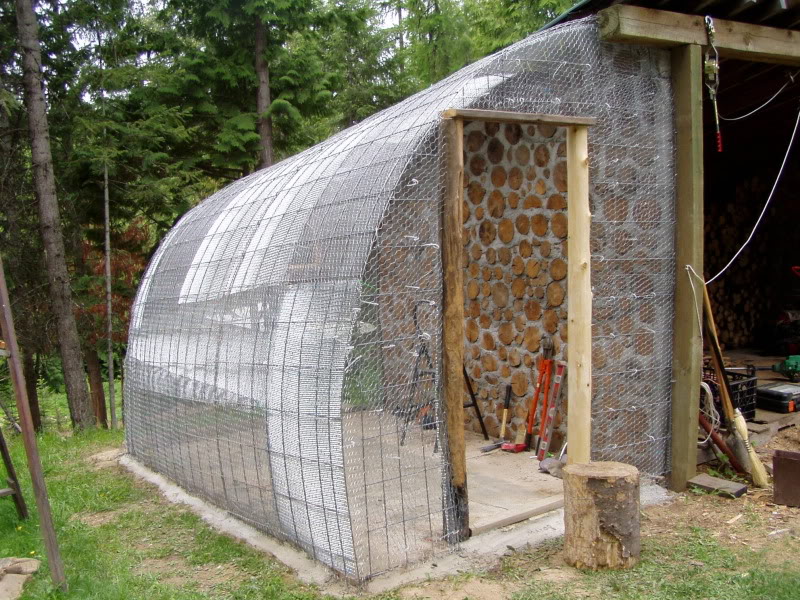
The Shed shrink
My five minutes with Ivan Dutton
The Shed’s resident mental health coach, Mark Seek, is constantly inspired by the many great people he comes across. One of his heroes is Ivan Dutton, now 83 years of age and still as active as ever. You will find Ivan an inspiration in the way he keeps illness at bay and lives life to the full rallying and repairing classic and vintage cars
“I retired at the age of 59 and let my son Timothy take control of Dutton Bugatti. He has done a fantastic job of building the business I started, and I was free to tinker with my own cars, bikes, and engines down in my shed.
I’m now 83, and have been having a whole new series of adventures with my friend Suzie. Her dad had cars like me but has Alzheimers. I started helping her out, and we’ve become inseparable. She is great at organising stuff, and I can cope with the mechanical and driving side of things – and I do as I am told.
Already this year, we’ve done loads of VSCC [Vintage Sports-Car Club] trials in my 1922 Salmson – Suzie does the bouncing. We’ve just been to the south of France to test-drive a Bugatti for my friend.”
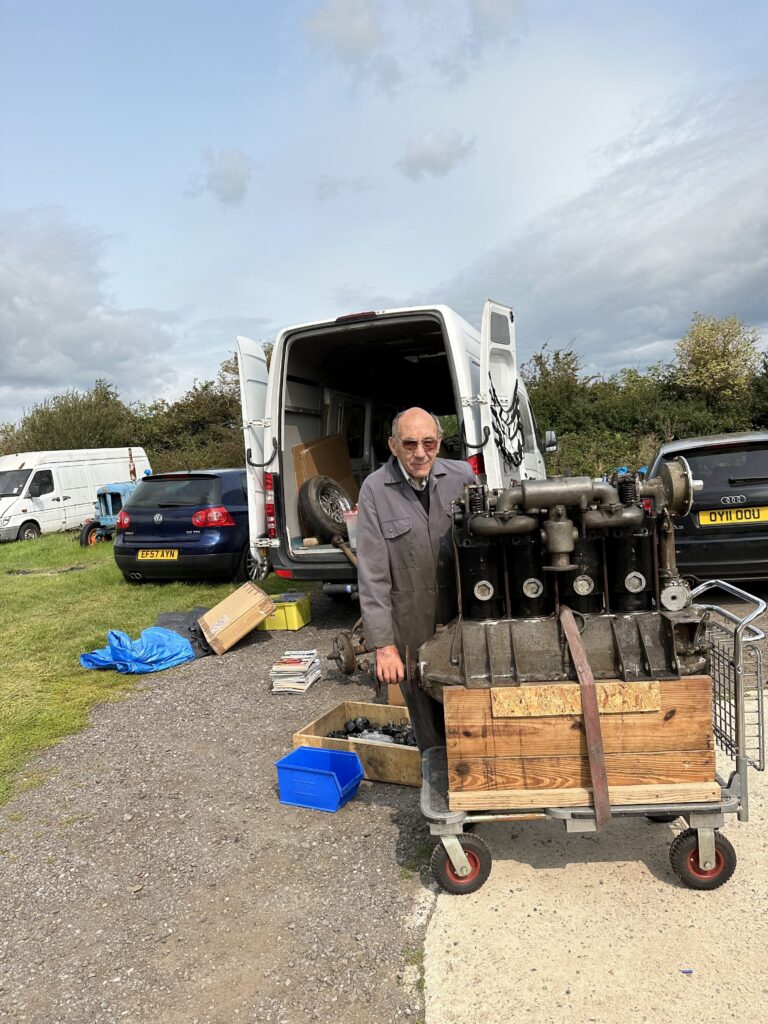
On the waterfront
The story of this venerable shed reflects the history of a whole district
On a trip to the Far North, The Shed’s Jason Burgess, came across an historic and quite magical shed on the side of the Hokianga Harbour. It eventuated that this was not just any shed but a working fishing business that has played a huge part in the district’s history and continues to do so. Welcome to the Hoki Smokey.
“When Nick quit diving, he joined the New Zealand Army as a combat engineer. He reckons the highlight of his service was spending two seasons on Antarctic operations. He served for 20 years before retiring from the military in the 1990s. Despite his years of globetrotting, Nick always knew that he would return to the Hokianga.
“Rawene was it; no other place in the world I’d rather be. With the skills I had, I went in with the old man – because he had sustained another injury. He fished all the time, but in the ’80s, when they brought in the quota management system, he got virtually nothing. I came home and invested a substantial sum in purchasing fishing quotas. I’m probably one of the larger private holders of fishing quotas.”
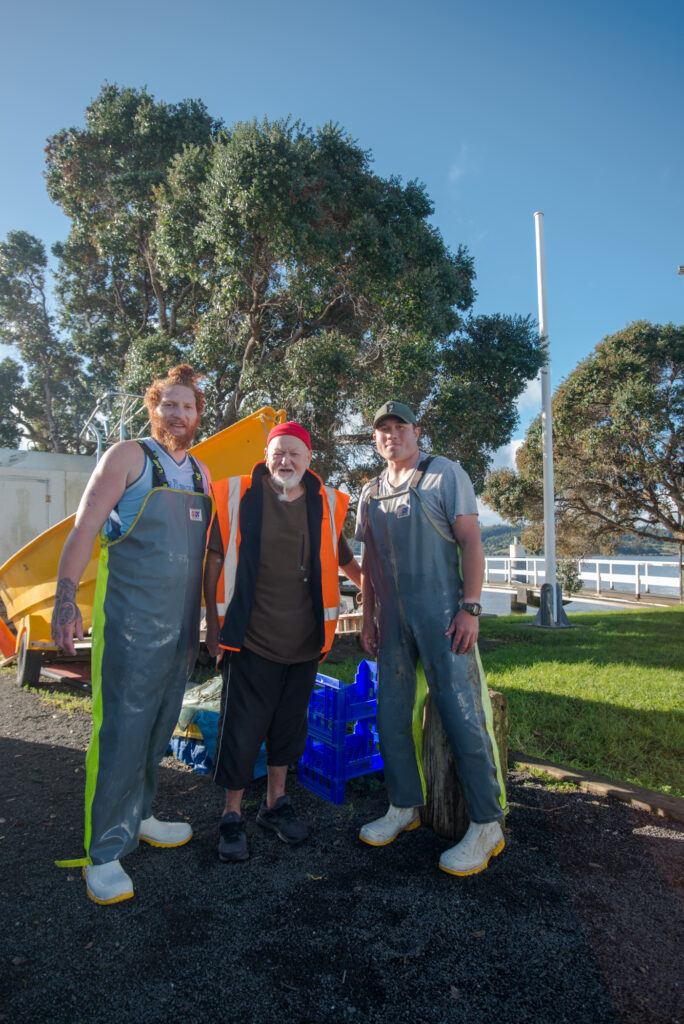
Back o’ The Shed: Instructions enclosed
All-too-often, assembly instructions can leave DIYers feeling as if they are the central character in a cartoon
The Shed’s founder Jude Woodside is busy on his rural property building and shed and completing projects galore. He is however somewhat grumpy about the supplied instructions with his new shed build. Instructions? What instructions?
“I have noticed a trend, especially in goods made in China or even Europe, for the instructions to be illustrations. Of course, that is fine if you can actually see what they are talking about. A case in point is this image from the plans for my shed. It’s an isometric drawing but to actually make sense of it requires a mental lurch. It’s not the best possible view of the piece; some shading would have helped.
Illustrations done well are a bridge between cultures, and far superior to the tortured English on Chinese instructions, which, I swear, are generated by either the Google algorithm or laborious consultation of a thesaurus.”
To purchase a copy of this issue, head to our online store
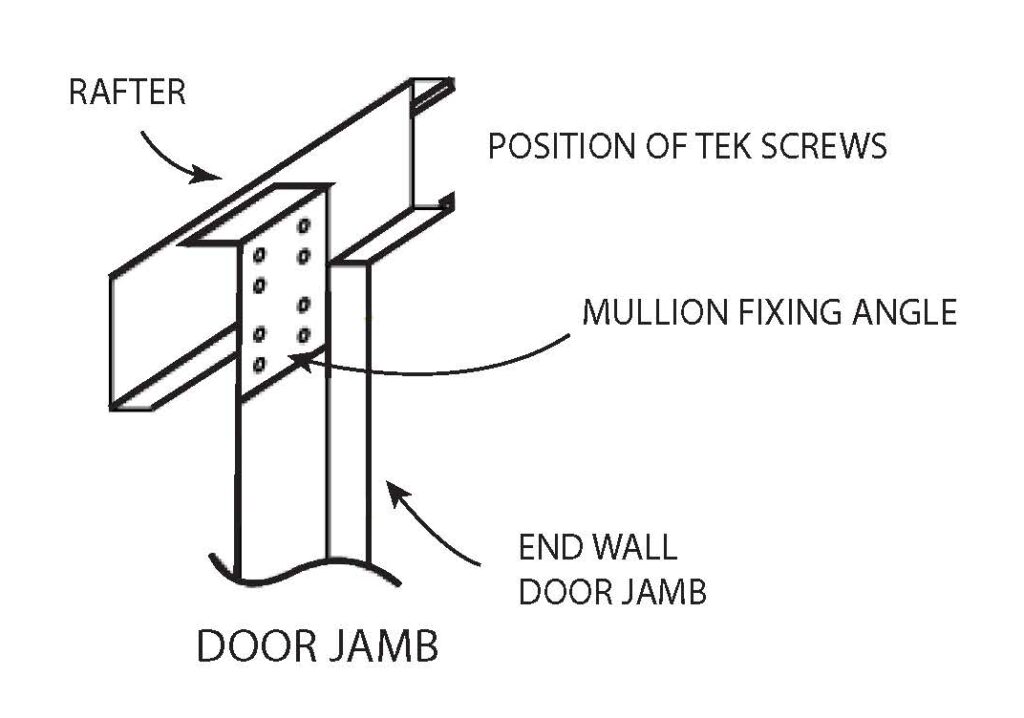